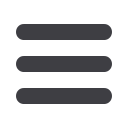
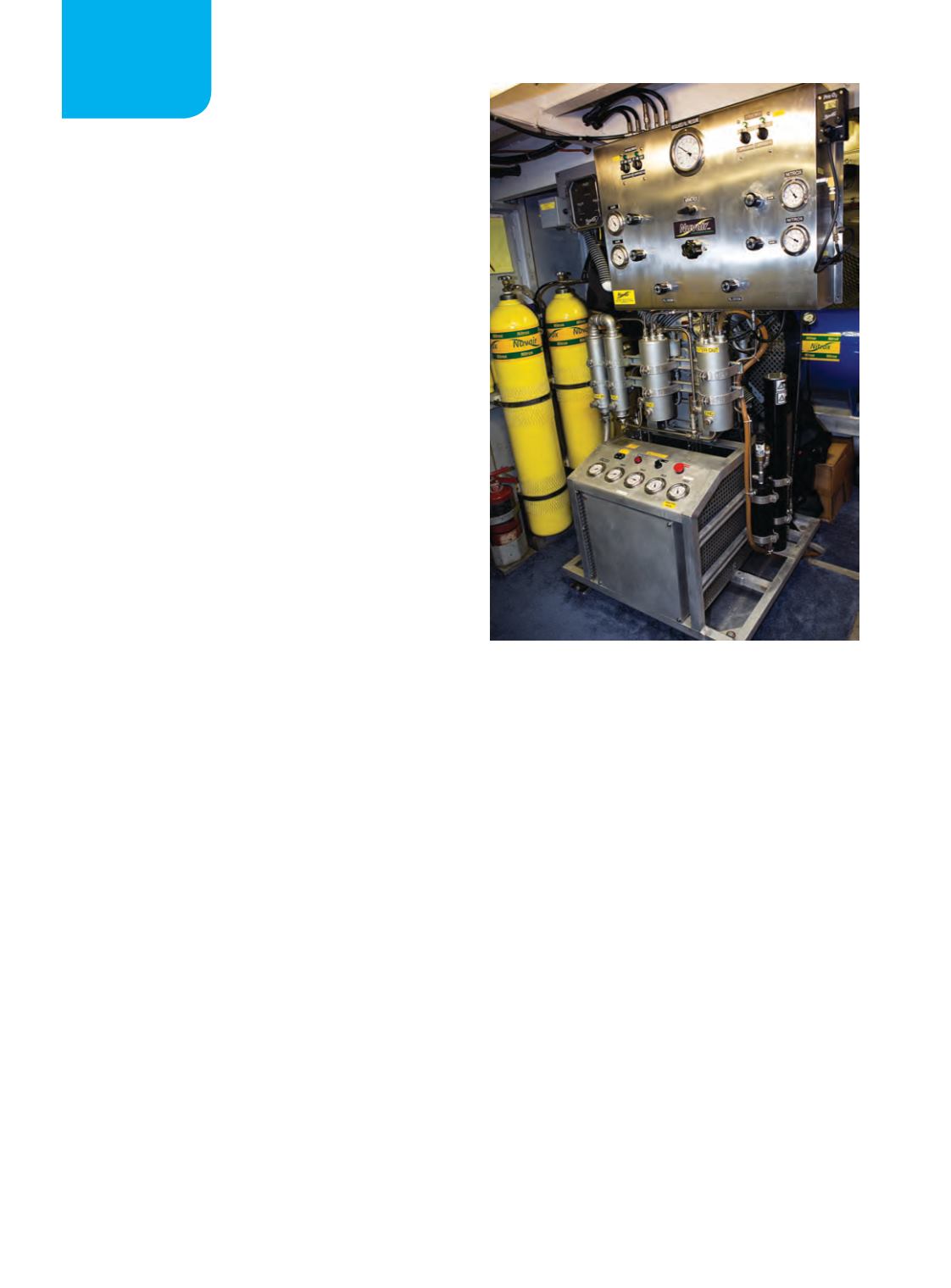
O
ne of the first things I tell students
in compressor maintenance classes
is this: “Providing breathing air
for consumption in an increased
partial-pressure environment is one
of the most invasive things you can
do to the human body.”
As most divers know, air is roughly 20.9 percent
oxygen and 78 percent nitrogen. The remainder
includes very small amounts of inert gases such as
argon and carbon dioxide (CO
2
). The air we breathe
on the surface also includes a small amount of water
vapor. As the air is compressed, the water vapor is
compressed into liquid water. Some oil mist (from
oil-lubricated compressors) is produced as well, along
with any gases or vapors that might have been drawn
into the compressor intake. The water, oil and vapors
are all considered contaminants and must be removed
to provide the diver with clean, breathable compressed
air. As the compressed air is breathed, the oxygen,
nitrogen and any impurities travel from the alveoli in
the lungs into the bloodstream and then to the body’s
tissues and cells.
There are basically two types of compressors used
for breathing air production: low pressure and high
pressure. Examples of low-pressure units (approximately
140 psi to 250 psi) are hookah rigs and hard-hat systems.
High-pressure units are used to compress air up to 6000
psi for filling scuba and storage cylinders.
The level of impurities in the final output of a
compressor depends on the type of purification system
used (if any) and how often the filters are changed.
Some recreational low-pressure compressors have
little or no filtration included. Diving depths with these
are restricted due to hose length and air production,
but one must still be very careful about what is drawn
into the intake, especially when it comes to carbon
monoxide (CO). CO, a product of engine exhaust, is
deadly and can be drawn into a compressor’s intake if
the intake is placed too near a potential source of CO.
High-pressure compressors, on the other hand, have
several stages that increase the pressure to levels that
allow the air to be pressed into scuba cylinders and/or
storage banks. Each stage compresses (and condenses)
the air, so the air must be cooled and the moisture/
oil mist captured, which is done with cooling coils and
separators. The separators must be purged in a timely
fashion — usually every 10-15 minutes, depending on
the humidity. This is done manually with many smaller
portable compressors but usually with an autodrain
system on larger stationary units.
The final air delivery then needs to be purified via
filtration. A typical purification filter will contain three
substances: a drying agent, activated carbon (to remove
remaining oil mist and odors) and a catalyst to convert
CO into CO
2
. The media inside a purification filter has a
useful limit, so proper filter changes must be conducted
based on the amount of air that passes through it.
There are other gases produced for diving, the most
common of which is nitrox. Nitrox (also known as
enriched air or EANx) is any gas mix that contains an
elevated percentage of oxygen between 23.5 percent
and 39 percent. Nitrox can be produced by the
following methods:
• Adding pure oxygen to a cylinder and topping it off
with pure air is called partial-pressure blending. This
procedure, like any process that requires handling pure
oxygen, presents an increased risk of fire, equipment
damage and serious injury or death and thus requires
specialized training and oxygen-clean equipment.
108
|
FALL 2016
GEAR
COMPRESSORS
THE ART AND SCIENCE OF
PRODUCING BREATHING GAS
By Rob Bleser
STEPHEN FRINK