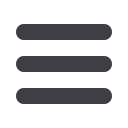
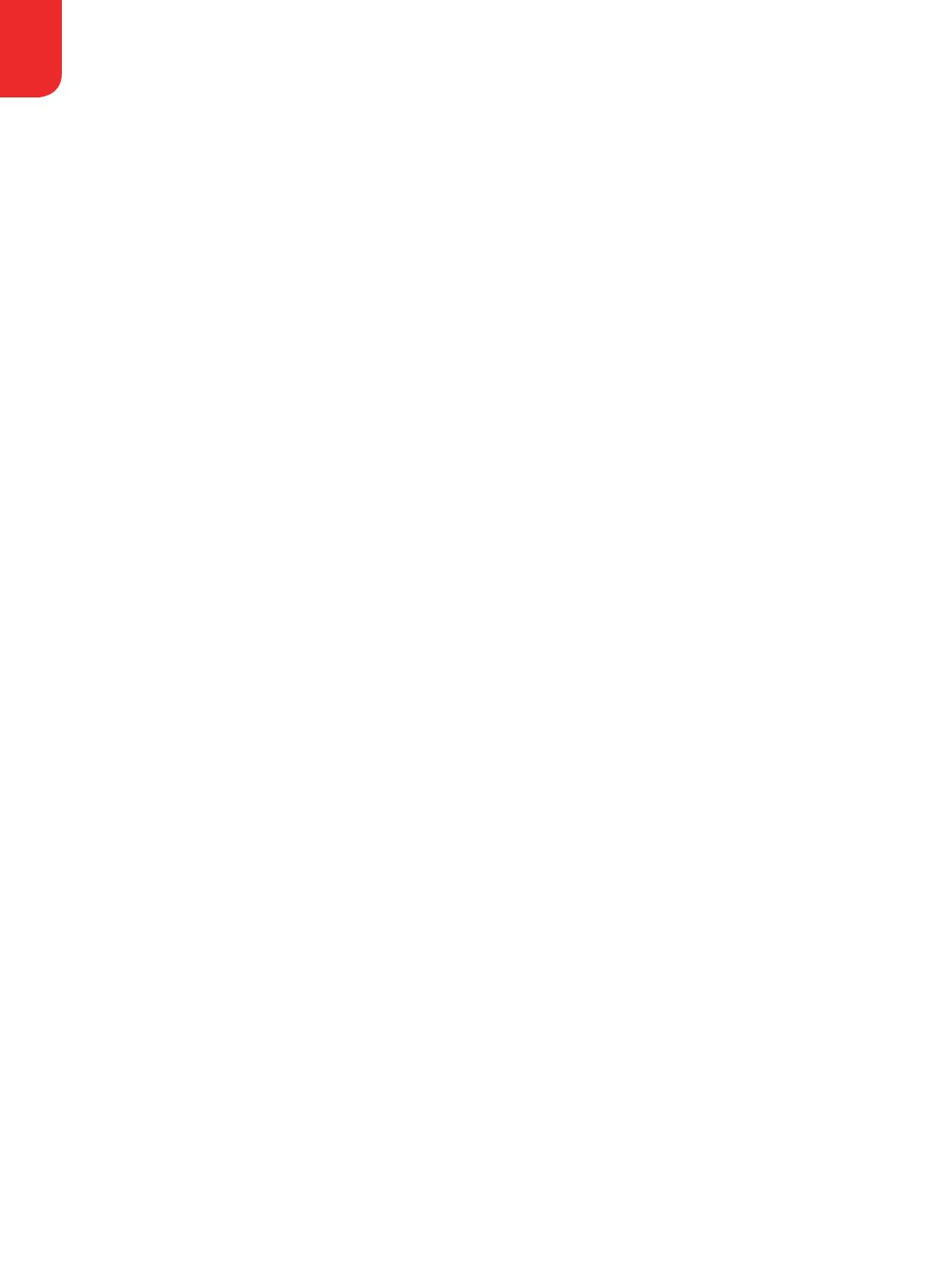
RESEARCH, EDUCATION & MEDICINE
ADVANCED DIVING
48
|
WINTER 2017
S
ome of mankind’s most amazing civil-
engineering structures are underground
tunnels and bridge foundations below
the water table. During construction,
the working spaces, or caissons, are
pressurized with compressed air to
keep out groundwater, and laborers (known as
sandhogs) pass though pressure locks into and out of
the caissons. In the 19th century, progress was rapid
until the workers were afflicted with a mysterious
condition called “caisson illness” when they returned
to atmospheric pressure. The Brooklyn Bridge was
completed before we learned how to prevent and treat
the pain, paralysis and sometimes death due to what is
now recognized as decompression sickness (DCS).
Caissons are dug vertically into bedrock to support
bridge abutments, while tunnels are horizontal and used
for roads, railroads, subways, water and sewage. Tunnels,
formerly dug by gangs of sandhogs using picks, shovels
and explosives, are now dug by tunnel boring machines
(TBMs), which have giant rotating cylinder heads with
toothed “faces” that cut through rock and muck as the
TBM is forced along. In favorable rock formations, only
the space in front of the TBM face is pressurized, and it’s
only occupied for maintenance and replacing teeth. This
limits pressure exposure and vastly improves safety.
IMPROVED TUNNELING EFFICIENCY AND SAFETY
When the 165-foot pressure limit for compressed air
is exceeded, alternative gas mixes must be breathed
to reduce the incidence of nitrogen narcosis, oxygen
toxicity and DCS. TBMs can accomplish this with
shorter working and decompression times. The
foundation for these improvements was laid in the
1960s when deep diving and decompression research
expanded in response to the need for offshore oil,
particularly with the Organization of the Petroleum
Exporting Countries (OPEC) oil embargo of the 1970s.
Saturation diving — in which divers remained at
pressure for a day or more such that their bodies
became equilibrated with the gas they breathed,
and they could remain at depth without incurring
additional decompression obligations — extended
divers’ reach in depth and time to 1,000 feet of
seawater (fsw) for weeks with few pressure-related
injuries. Experience taught how heliox (helium-oxygen)
and trimix (helium-nitrogen-oxygen) could be used
at greater depths, how nitrox (nitrogen-oxygen) with
more than 21 percent oxygen (oxygen-enriched air,
or OEA) could be used at intermediate depths and
how 100 percent oxygen could be used during shallow
decompression. These techniques made for enormous
improvements in productivity and safety.
Surface decompression (decanting) is another
technique used widely in military and commercial diving
to limit time in the water, where keeping warm is difficult.
The diver remains at about 40 fsw before ascending to
the surface in 1 minute, entering a deck decompression
chamber (DDC), being pressurized back to 40 fsw
in the DDC, breathing oxygen to clear inert gas and
decompressing to the surface. Surface decompression
is also useful in tunneling and caisson projects in which
workers decant from an intermediate pressure of about
18 pounds per square inch gauge (psig) or 40 fsw, dress
comfortably, enter a DDC and are repressurized to 18
pounds per square inch (psi) for decompression.
Another useful method developed in the 1960s and
’70s was saturation-excursion diving, in which divers
lived in an underwater habitat or DDC and made
excursions to greater depths and then returned (with or
without decompression stops) to the saturation depth.
Decompression to the surface was postponed to a later
day. For deep excursion depths, trimix might be used
as the breathing gas with careful monitoring of the
oxygen exposure history to avoid oxygen toxicity.
TUNNELING AROUND THE WORLD
The use of mixed gases for higher-intervention-
pressure civil-engineering projects is more common
in Europe and Asia than in the United States. Projects
include deep shaft sinking at 4.8 bar (157 fsw) in the
Netherlands, 5.8 bar (190 fsw) for subways in Russia
and Seattle and 6.9 bar (225 fsw) in a Netherlands
tunnel. The Western Scheldt tunnel project in the
Netherlands used trimix at 4.8 bar (157 fsw) with
saturation-excursion decompression. Mixed gases
Caissons, Compressed-Air
Work and Deep Tunneling
By David Kenyon, Glenn Butler and Richard Vann